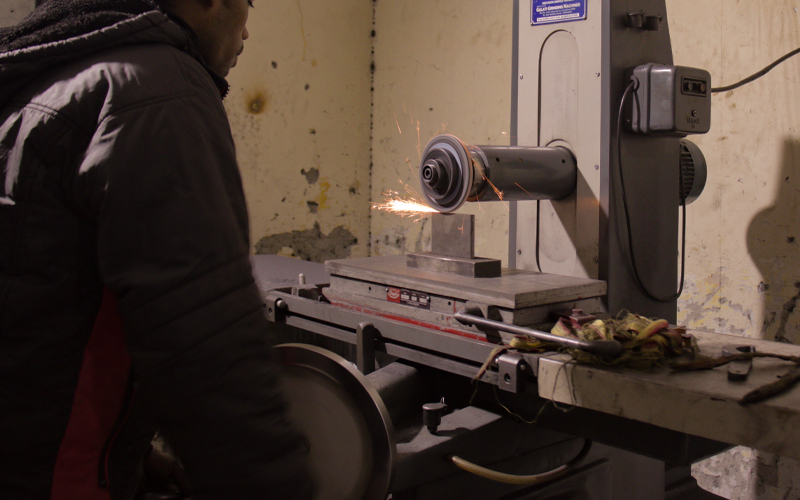
The raw materials come in standard sizes and are required to be fed into cutting machines to get the desired shape and size.
• Machining is the broad term used to describe the removal of material from a workpiece
• Includes Cutting, Abrasive Processes (grinding), Advanced Machining Processes (electrical, chemical, thermal, hydrodynamic, lasers)
• Automation began when lathes were introduced in the 1700s
• Now have computer numerical control (CNC) machines
• Machining operations are a system consisting of:
• Workpiece – material, properties, design, temperature
• Cutting tool – shape, material, coatings, condition
• Machine tool – design, stiffness & damping, structure
• Fixture – workpiece holding devices
• Cutting parameters – speed, feed, depth of cut
Types of Machining Process
• Single Cutting Edge (Point) Processes
• Multi-Cutting Edge (Point) Processes
• Random Point Cutting Processes – Abrasive Machining
• Within each category the basic motions (kinematics) differentiate one process from another
For Your Information:
To meet and exceed customers’ requirements. • Continuous up-gradation in technology to achieve zero defects. • Team Work and zilch defect delivery for a better experience.
Our labs are validated with high-end types of equipment. • Experienced workforce and ultra-modern manufacturing facilities. • To produce consistent quality of components, value for money, & ensure timely delivery.
Visual Inspection is done after the innovation process to ensure zero defect part supply.